The Prescient Data Center Manager
How to predict standby battery life.
Today’s modern UPS systems employ cutting edge
technology, and it is tempting to believe that
deploying that technology is enough to protect
mission-critical applications from a power outage. But
here’s a simple truth: the UPS draws its power from banks
of lead acid batteries, and those batteries can go from
good to failing in a matter of days. Even the latest and
greatest UPS system provides no protection without fully
functioning batteries.
There are a number of ways to manage and maintain
the batteries. The available labor resources, cost, and the
importance of the load the batteries support all influence
an organization's choice of techniques.
Labor resources not only include the amount of labor
available but the quality of that labor and other cultural
concerns. For instance, in some nations labor is plentiful;
battery maintenance and monitoring often is carried out
continuously and by hand. In some of these regions, the
staff is reluctant to bring bad news to a manager, especially
if the messenger was supposed to maintain the prematurely
failing batteries. In other societies, organizations
cannot afford a staff to continuously monitor batteries.
Most professionals would like to be able to see into the
future to know when their batteries would fail. Instead
many companies replace 10-year life batteries every three
to five years. They try to anticipate the failure of their
batteries; they try to peer into the future. A review of
battery monitoring and maintenance methods shows that
professionals do have the ability to look at historical data
right through to looking at predictive data.
Historical Failure Rates
Organizations that keep good records know the age of a
battery that dropped a load, dumped the prime web site,
lost customer dollars, lost a client, and cost someone a
job. Battery replacement is based on the principal that new
batteries should be installed just before the age they were
when they failed last time. But what happens if the data is
not available?
Checking batteries once a year tests to see if the battery
failed during the preceding 12 months. This is looking into
the past to try to avert future problems. A lead-acid battery can go from useful to useless in less time than it takes to
order up a replacement and schedule the people to come
out and fit it.
Valve-regulated, lead-acid (VRLA) batteries often cannot
take the load at time of install. Some of these batteries
recover over the first three months of life, sometimes they
just don’t. Others fail in a matter of 10-15 days during the
remainder of their life. Scheduling more frequent testing
is little help, as they could start to fail the day after the test
and be useless in time of need, two weeks later.
Also consider the nature of the test. The portable handheld
tester has a number of shortcomings. The condition
of the cables used, or more specifically, their state of
repair can affect the result considerably. Many working
and good batteries have been replaced by accident instead
of replacing the test leads. How the cable connectors are
put on the terminals also affects the results, either way.
These days many VRLA batteries do not have connection
terminals big enough to accommodate a test clip.
The quarterly visit can introduce other problems. Some
refer to the routine maintenance schedule as planned
destructive maintenance, because equipment that is working
perfectly well can be affected by tampering during
maintenance. Frequently (more often than most battery
technicians would like to admit) breakers get left open,
intercell straps are left off, plugs are left open and bolts
left finger tight.
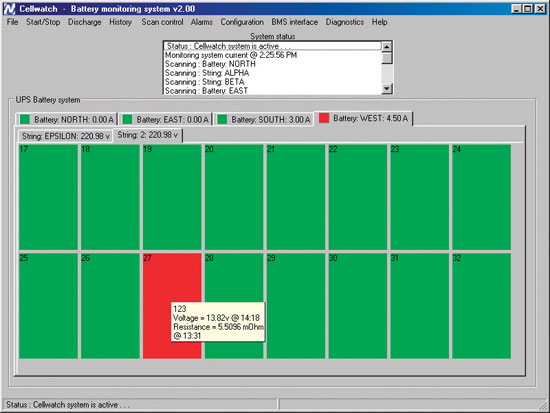
Figure 1. Modern battery monitoring systems can show at a glance if a battery parameter exceeds a threshold and
requires further investigation. This screen shot shows a string of 40 jars with one in alarm mode (red).
The Alternative
A permanently connected monitoring system can replace
the hordes of workers needed to manually monitor batteries
in low-cost labor regions, with additional benefits.
The first step is to install a battery monitoring system and
understand how it works and how to use it. Knowing how
to adjust it when necessary is critical.
But can the monitoring system tell an organization
anything useful about the future?
The answer requires thinking about the periodicity of
the measurements and what parameters the monitoring
system measures. A permanently
wired battery-monitoring system
would be better
than a handheld device carrying out the same tests every three months
because variability of connections and doubt concerning
the state of the test leads would be removed from the equation.
But why stop at quarterly tests? Surely the more data
points the wired system can gather and compare the better
the detail. More detail helps identify problems earlier
before batteries fail.
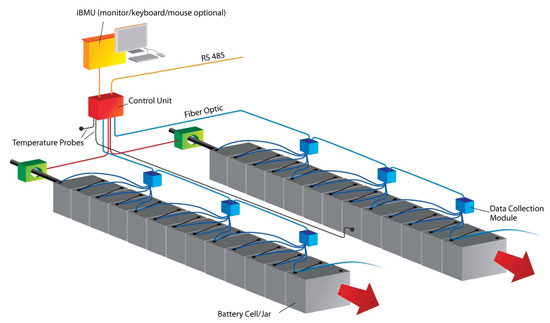
Figure 2. A permanently wired battery monitoring
system featuring data collection modules (DCM) attached
to each battery cell/jar. Each DCM is connected by fiber optic cable to
a control unit that transmits data to a dedicated PC (iBMU). Modern systems
will also expand to include generator and switch gear/telecom batteries.
Ideally, a permanently wired battery-monitoring system
enables readings of the float voltage of every component
of the battery every day. That includes every
cell, block, jar, or even smaller
minimum changeable component
of the battery. If over several
days the float voltage of a cell
trends downwards compared to
others on the string, the system
has identified a problem. Finding
a problem means that the battery
should be investigated without
panicking. The battery may need
replacing, but other outcomes are
possible.
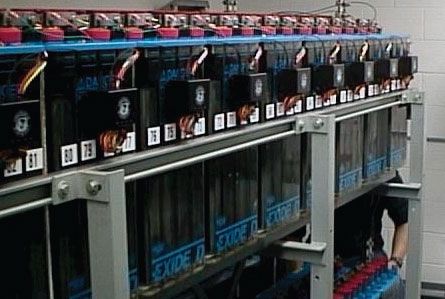
Figure 3. This installation shows a permanently connected (OV) battery monitoring system installed neatly
onto the battery.
Is the float voltage related to
the performance of the battery?
It can be, meaning that it can also
be unrelated. In general the float
voltage of a bad cell will be lower than its peers. But sometimes
the cell has to have become useless before voltage
alone can be used to identify it. So what then? The answer
is Ohmic Value.
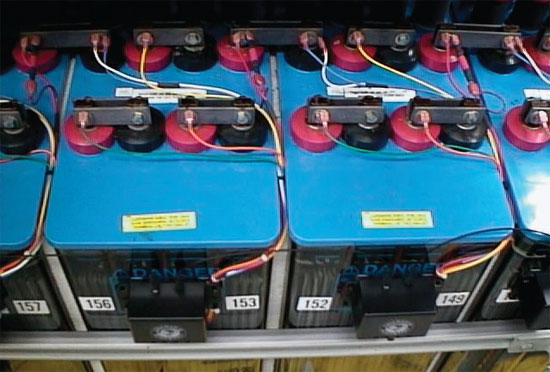
Figure 4. Data collection modules (shown attached at the front side) collect information including Ohmic
Value and voltage data from each battery cell/jar and transmit it to a dedicated PC.
Ohmic Value
Before Ohmic Value, users could measure resistance,
impedance, and conductance. The proper use of these
metrics confused users, leading to a number of white
papers and perhaps even some bad blood between proponents
of competing techniques.
IEEE developed the concept of Ohmic Value (OV)
to clear up the confusion. Ohmic Value is a figure that
indicates how the battery behaves under a small load. The
figure is not an absolute, comparable figure, but a relative
measurement. It is relative to the OV on the battery when
new and the OV of all the other cells in the battery.
Typically OV will rise and be detectible as faulty three
months before voltage falls and is visible as faulty. The
owner of a wired-in system with Ohmic Value has at
least three months better forward vision than a system
that relies only on voltage. The key is to be aware of the
periodicity of OV measurements.
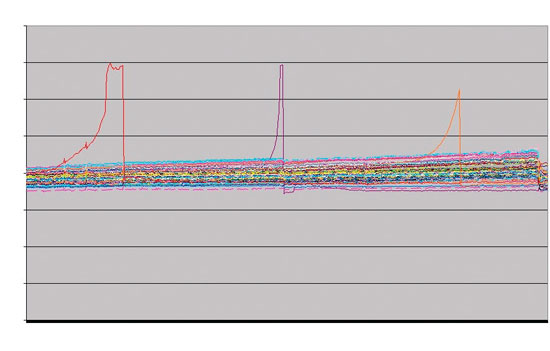
Figure 5. This report shows historical OV data for three years of a battery’s life, including three instances of battery failures and replacements. Notice in particular how much more quickly the
data center manager replaced the faulty jars as time went by.
If 12-volt VRLA blocks can go bad in 14 days, then
OV must be measured, recorded, and compared (analyzed)
every day. This frequency provides sufficient time
to investigate, order, and replace parts before the power
system integrity is put in jeopardy. ‘Every day’ measurement
of OV didn’t become practical until recently. To
measure OV, a current must either be injected into the battery
or removed from the battery for a very specific and
accurately measured amount of time. During this process
voltage readings are taken and compared to voltage readings
taken immediately before the test took place. The
difference between these voltage readings indicates the
Ohmic Value of the cell or battery. Unfortunately removing
a large amount of current from the battery or removing
it for an extended period of time can cause problems
in a parallel/string charging arrangement that can result
in damage to the batteries. To avoid this damage, early
versions of wired systems with OV measurement capability
took readings only monthly or every two weeks. Once
again there is a period during which a battery could fail
and the load could be dropped.
The amount of current used in the test has been the
barrier to more frequent testing. The greater the current
the less frequently the test can take place. So a very
small current would be best. But changes in voltage from
a very small current applied to UPS-sized batteries are
almost impossible to measure, especially with a UPS
charger and inverter running on the same power line.
The electrical noise, ac ripple, and switching pulses
swamp the tiny signal.
Electronic engineers eventually found a way to discriminate
the tiny signals produced by smaller amounts
of current for very short periods of time. This task is still
difficult, especially if the measurement signals are backed
onto the noise output from a UPS and requires a modern,
state-of-the-art battery monitoring system.
A wired system removes the variability of test leads
and the risks of human error, eliminating once and for all
planned “destructive maintenance.” Ohmic scans provide
voltage trending three months earlier than previously possible,
and daily scans identify the day that a battery starts
to trend away from its correct value compared to when it
was new or compared to its peers.
The final detail is that the battery monitoring system
must have the ability to turn itself into a voltage datalogger
the moment the battery goes on-line. This datalogger
then must take a battery reading every few seconds on
each and every cell for the duration of the discharge. Then
it can provide documented evidence of the value of an
investment in a proper wired, predictive, battery monitoring
system that can measure Ohmic Value.